Have A Question?
How Often Should Your Electrical Equipment Be Tested and Tagged
In many industries, electrical equipment is used to perform different operations or help complete a process. These operations or processes don’t happen all the time. Instead, they’re only done when they’re necessary.
Even though electrical equipment isn’t used as frequently as some other types of equipment, it still needs to be tested and tagged to comply with various regulations. Many different requirements depending on where in the world you operate your business. This blog post discusses some of the main requirements that electrical appliance or equipment testing and tagging have, depending on your environment or equipment.
What is testing and tagging electrical equipment?
Testing and tagging electrical appliances or equipment is a process that ensures electrical equipment is safe for use. This is done by checking the condition of the equipment and verifying that it meets technical standards.
Purpose of Electrical Equipment Testing and Tagging
Testing and tagging electrical equipment is an important part of maintaining workplace safety. It's required in many industries. Testing and tagging are important to help prevent injuries or possible accidents when the equipment is used.
The purpose of equipment testing and tagging is to keep workers safe by ensuring that the equipment they use is clean and safe to operate. This can be done by using a tester to verify that the equipment has no voltage or current running through it, followed by tagging it with an approved tag so that other workers know it has been tested and found safe for use.
Test and Tag Frequency Explained
Electrical equipment must be tested and tagged depending on Australia's requirements. The test and tag frequency, otherwise known as test and tag "intervals", refers to the time between safety inspections of an electrical appliance.
It's important to keep in mind that some businesses do their own risk assessment. This means that they might test and tag more often than what is specified. This is fine, but testing less often is not acceptable.
Here are the intervals you should be aware of according to AS/NZS 3760:2010 - Table 4:
Test and Tag Inspection Intervals for Electrical Equipment
(Caution: This page must be read in conjunction with AS/NZS 3760 as a whole and particularly 2.1)
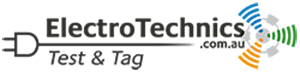
Frequency for Construction Sites, Demolition and Mining Industries
For equipment used in a construction, demolition or mining environment, the recommended test and tag frequency is every three months because of its high-risk environment. In addition to the 3-month interval, the specialist will need to use particular test and tag colours to keep track when the equipment was last tested.
Frequency for Hire Equipment
For electrical hire equipment, it must first be visually inspected and tested and tagged every three months.
In terms of who actually performs the testing, it is determined by a few factors. It will be the hirer's responsibility if the hiree has the necessary equipment for at least 3 months (otherwise it would rest with the hirer).
Who can test and tag electrical equipment?
In order to test and tag equipment, the specialist must be qualified and hold a current license. The qualification must be from an accredited institution.
The specialist will also need the right tools to do the job. These include:
- an electrical tester - used to measure the strength of the current running through the appliance
- a multimeter - used to measure the voltage;
- a portable appliance tester - used to test the appliance for earth leakage
- an insulation tester - used to check for any current running through the insulation of the appliance.
After the specialist has tested the equipment, they will need to tag it. The tag must include:
- the date of the test
- the name of the specialist or the company that did the test
- the next due date for testing
- the tag must also be made of an approved material, such as vinyl or plastic.
Testing and tagging equipment is a vital part of maintaining workplace safety. The test and tag frequency will vary depending on the environment or equipment. It's essential to have your equipment tested and tagged by a qualified specialist to help prevent injuries or accidents in the workplace.
Benefits of Hiring Professional Electrical Equipment Testers
If you have electrical appliances or equipment in your business, you need to make sure that it's tested and tagged by a professional. This will help you avoid large fines and any potential injury to your employees or customers.
Hiring an electrical equipment tester is worth the investment at the end of the day. They will do the work for you so that your business can remain compliant. If you have some questions about what needs to be done with your equipment, they should answer them for you.
In addition, they should be able to provide documentation of all their test and tag services. This will come in handy if you ever need to prove to an inspector that your equipment is up to date.
Don't forget that electrical safety is not something to be taken lightly. It's always better to be safe than sorry when it comes to dealing with electricity. Test and tagging your equipment is one way to help ensure that everyone in your workplace remains safe.
Bottom Line
Test and tag is a process where your electrical equipment and portable electrical devices are checked to ensure that your equipment is free of electrical risks and safe for use by your employees. Frequent testing and tagging is a good way to stay on top of your workplace's electrical safety, especially if you're in a demanding industry.
It's always best to hire a trusted professional for regular testing of your electrical appliances, devices, and systems.
At iTAGPRO, we offer a wide range of services, including electrical equipment test and tag, plug and electrical cords repair, safety switch testing, and more. Contact us today to learn more about how we can help you ensure the safety of your workplace.
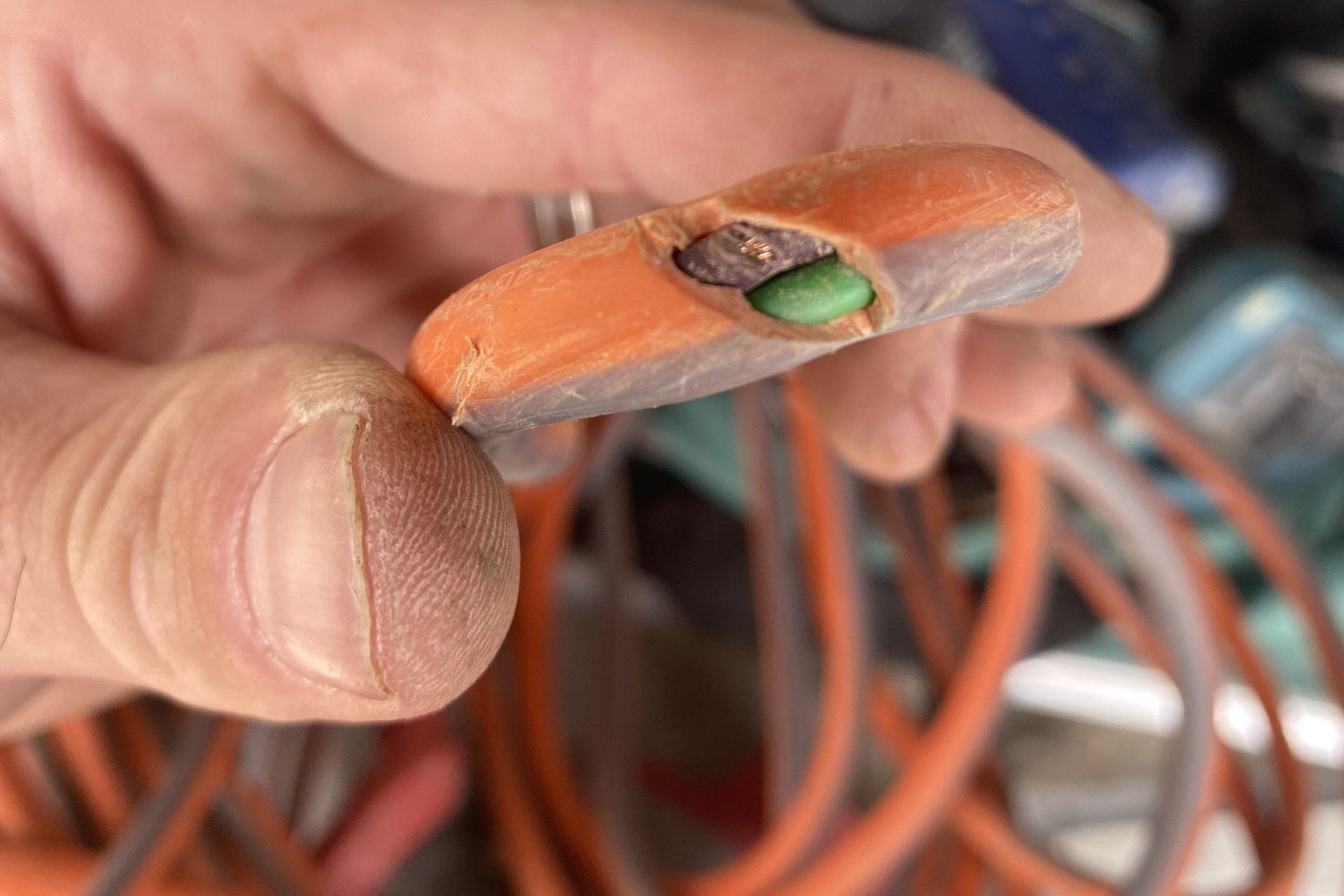